How Do Hydraulics Work? What You Need To Know
-
Pete Ortiz - Last updated:
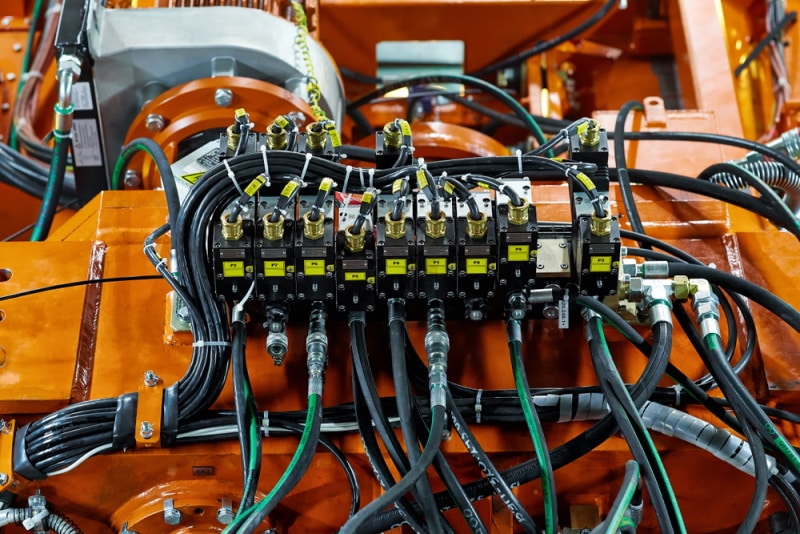
Hydraulics are everywhere and facilitate how societies work, travel, play, and operate in daily life. From our vehicles to the heavy equipment that builds our homes, these centuries-old principles power modern machinery to make our lives easier and safer.
While we enjoy their benefits nearly every day, it’s easy to under-appreciate or misunderstand the hydraulic systems around us. Let’s explore the cleverly simplistic science that makes hydraulics work.
How Does It Work?
Hydraulics operate on the principles of Pascal’s Law. Blaise Pascal stated that pressure on an incompressible fluid transmits evenly in all directions throughout the fluid. In a container, any pressure change on the fluid will occur undiminished at every point.
We can witness Pascal’s law at work with a simple syringe or U-tube with pistons on each end. If you fill an oral syringe with air and plug the end, you’ll be able to press the plunger in a bit before it stops. Air is compressible, allowing you to push the syringe even while blocking the end.
If you fill the syringe with water and plug the end, you won’t be able to press the plunger even a tiny bit, as the fluid is incompressible. Instead, the pressure at the plunger transmits across the rest of the liquid, exerting itself equally against the walls. When you release your finger, fluid will erupt out of the open end immediately.
In a U-tube with movable pistons plugging the ends, you can see the basics of another practical side of Pascal’s Law. As one piston compresses, it applies pressure throughout the fluid. The pressure creates a 90-degree angular force against the container walls, one of which is the other movable piston. With pressure acting on it, the other piston pushes out.
Pascal’s Principle and Practical Applications
The change in hydrostatic pressure related to Pascal’s Law is equal to the force divided by the unit area where it is applied (P=F/A). For example, a 10-pound weight on a 10-square-inch piston surface would change the pressure by 1 psi throughout the system.
Since the pressure change is the same at all points across a contained fluid (P1=P2), the force against a larger surface area would have to be that much greater (F1/A1=P=F2/A2). That 1 psi of added pressure from the 10-pound weight on one piston would lead to 100 pounds of force against a 100-square-inch piston surface.
With that principle in mind, you can see that a lighter input on a smaller piston can generate an enormous force on a larger piston. You can lift incredible weights with minimal effort by magnifying the force with more area.
Note that the basics of hydraulics surround the flow and pressure change rather than the pressure of the fluid, which will vary according to depth and atmospheric pressure. While you may be able to manipulate those factors to make lifting easier, hydraulics deals primarily with changing pressure to move fluids and transfer energy.
How Force Affects Distance
The output motion distance has an inverse relationship with the force acting upon the actuator. Although a small input on a smaller area can add more force to another surface, it can’t create more work.
Work is equal to force times distance. To make up for the added force that a smaller input generates on one end, the larger end of a hydraulic system moves a proportionally lower distance. For instance, if a 10-pound weight on a piston in a U-tube creates a 20-pound force on a larger surface, that side would only move about half the distance of the 10-pound side.
Because a piston on the small end of the hydraulic system has a limited space it can travel, it is often impractical in applications requiring extreme power. The movable distance of the larger side, which can have areas hundreds of times larger than the input side in presses and lifts, would be minimal, even with the input piston traveling a long distance.
Most hydraulic systems account for this by using a pump on the input side to feed the line continuously and build pressure. With a pump, you can keep moving the actuator end as long as the fluid is available in the reservoir.
What Are the Different Types of Hydraulics?
A hydraulic system consists of several parts that contain and move liquid via pressure applications. Mechanical energy on one end converts to hydraulic energy and back to mechanical energy at the actuator. The mechanical energy output could be linear, like a piston in a cylinder or rotational, as you would see in a hydraulic motor. Hydraulic systems generally consist of four essential components:
- The pump inputs energy to move and pressurize fluid throughout the system
- A reservoir containing the hydraulic fluid
- Valves to stop and direct the flow of fluids through the system and relieve pressure to prevent damage
- Actuators that convert hydraulic energy to mechanical energy
Systems can vary based on the type of pump. These include screw pumps, piston pumps, vane pumps, or gear pumps.
Open vs. Closed Loop Hydraulic Systems
We can also define hydraulic systems as open or closed loops. In an open loop system, the fluid moves from a reservoir to a pump and on to an actuator. With the tank, the fluid can dissipate heat and allow any contaminants to settle before running through the pump again. An additional directional control valve lets the operator change the motion of the actuator.
Closed loop systems eliminate the reservoir, instead including speed and direction control at the pump. A displacement control lever attaches to a swash plate that controls the flow to the actuator. As the lever moves forward, the swashplate changes angle, increasing the flow and the actuator speed. The lever can also sit in a neutral position to halt the flow and turn in reverse to change direction. While there isn’t as much heat dissipation, closed-loop systems provide precise control and a more compact setup.
Where Is It Used?
You can find hydraulic systems at work in countless settings, including heavy machinery, vehicles, and aviation equipment. A simple example of hydraulics you likely use every day is your car’s braking system. Your foot presses the brake pedal, compressing fluid in a tube at a small piston. The added pressure to the hydraulic fluid transmits to a piston at the brake caliper, causing the brake pad to squeeze against the rotor and slow the car.
- Hydraulic car suspensions
- Gas pumps
- Forklifts
- Vehicle lifts at service centers
- Cranes and other heavy construction equipment
- Elevators
- Barber chairs
Advantages of Hydraulics
Hydraulic systems are simple to use and allow for accurate movements. Energy generation and transmission are easy across varying distances and paths in a flexible setup with durable tubing. Compared to pneumatic systems, which only produce roughly 80–100 psi, hydraulics operate at 1,000–10,000+ psi for enhanced lifting power. Hydraulic oils also make these systems self-lubricating, and the limited moving parts make them lower maintenance and safer across hazardous settings.
Disadvantages of Hydraulics
The primary downside to a fluid-dependent system is the risk of leaks, which will shut down the hydraulic power and present potential safety and environmental issues. Fluids can also accumulate contaminants, requiring filtration and regular maintenance to ensure ongoing performance.
Frequently Asked Questions (FAQs)
What Kinds of Fluids Do Hydraulic Systems Use?
Hydraulic fluids serve several purposes in a system. Along with transmitting pressure, they can decrease wear through lubrication, corrosion prevention, and heat transfer. Quality fluids also limit contamination within the various hydraulic components. The following are the most common types of hydraulic fluids in use:
- Petroleum or mineral-based fluids: The most widely available fluids offering a low cost, high quality, and diverse selection
- Synthetic fluids: Man-made fluids with excellent lubrication, fire resistance, and stability under high temperatures and pressure
- Water-based fluids: Water and oil blends with good fire resistance but lower lubrication and wear resistance
The proper fluid for a hydraulic system depends on several properties, such as viscosity, stability, and oxidation resistance. Viscosity relates to the fluid’s flow resistance, a crucial consideration in hydraulics. A high-viscosity fluid will need more energy to flow. If the viscosity is too high, the system will lose efficiency and become more prone to wear. When it’s too low, the fluid loses lubricity. The viscosity index relates to how viscosity changes with temperature. Some fluids keep their optimal viscosity across a broader range for better performance.
- Detergents
- Anti-wear and anti-rust compounds
- VI enhancers
- Defoaming agents
Petroleum and mineral-based oils often contain additives to improve performance and overcome their unique drawbacks. For instance, detergents can reduce sludge buildup, while VI enhancers maintain the system’s efficiency in more extreme temperatures. Many also utilize bright dyes, making leaks easier to detect and helping you avoid costly repairs or accidents.
Conclusion
Hydraulics have been integral to how machines operate for generations, and innovators continue to find ways to apply Pascal’s findings to current technology. Take a second to seek out the hidden, everyday hydraulic systems that help you function to discover how much we truly owe to these simple principles.
Featured Image Credit: Aleksey Telesh, Shutterstock
Contents