What Are Galvanized Screws? Uses, Parts, & Types
-
Pete Ortiz - Last updated:
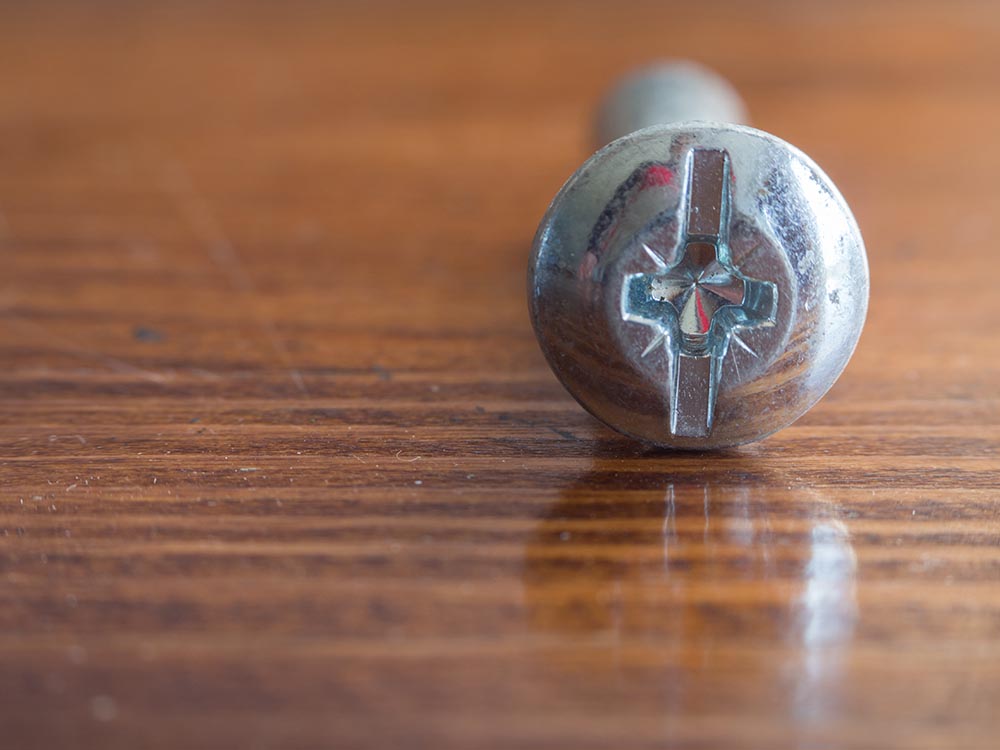
If you are into woodworking or mechanical parts maintenance, you know the importance of getting the right tools to do a job. For instance, when working with wood, you have to know when to use a nail or screw to hold two pieces together. As with mechanical parts, you have to use the correct type of screws for parts to function and last a long time.
Screws are a simple invention that revolutionized how things are put together. But this should not fool you into thinking that they are simple by any means. Screws come in all shapes and sizes and are made from different materials for different applications.
Galvanized screws are steel screws coated with a zinc layer through an electrolysis process or hot dipping. This helps protect the steel underneath and extends the lifespan of the screw while in use. In addition, galvanization reduces degradation when a screw is exposed to the elements.1
This article will look at galvanized screws, how they are made, and what you can use them for.
How Are Galvanized Screws Made?
As with any other type of screw, galvanized screws are made from cold forming. This usually involves shaping a piece blunt piece of wire into a screw by forcing it through screw-forming dies. However, the process starts by feeding a large roll of wire through a machine that straightens it, cuts it into size, and feeds it to the die.
Then, the machine punches the wire to form it into a recognizable screw shape. However, the screw is yet to be fully formed at this point as it’s still smooth and unthreaded. This leads us to our next process, which is thread rolling.
Thread rolling uses dies that have been manufactured to the thread pitch required for the screws being made. The smooth screw is sandwiched between the two dies. One is stationary, while the other moves. The moving die uses pressure to push the screw against the static die while rolling it between the two from one end to the other. Leaving the desired thread indentation on the screw as it is ejected.
Now the screw is formed, but it still has to go through one last process known as hot-dip galvanizing. This involves dipping the screw in a molten zinc bath for several minutes to allow the zinc to bond to the surface of the steel screw. After dipping, a protective layer is formed around the screw, which helps it withstand the elements better.
Because zinc is more corrosion-resistant than steel, it keeps a screw from rusting when it is bonded to its surface. It also reduces the maintenance requirements of any steel structure as well as preserves it for longer.
Parts of a Galvanized Screw
A screw is a short piece of a sharp, threaded, cylindrical metal shaft with a slotted head. It holds two objects together by twisting them through one and into the other. In addition, most are also designed as self-driven, which essentially means they cut into the material as they are twisted and driven in.
A screw has different parts that allow it to function, which we will highlight below.
1. Head
This is the top of the screw that is the main part and also broader than the shaft. Its size varies according to the screwdriver used to tighten or loosen it. It’s also the part that’s left exposed after the screw is driven in for reference purposes.
2. Drive
The drive is also known as the screw head or, to be more specific, the indentation on the screw head a screwdriver inserts into to twist. Screws come with different drives, so it’s good practice to have multiple screwdrivers with varying types of heads. In addition, the drive is also the part that helps you to twist a screw into position.
3. Threaded Shaft
This is the part of the shaft with a sharp tip and helical grooves that allow a screw to bore a hole and grip whatever it’s being driven into. The threads also generate the friction needed to hold two things together using the screw.
4. Non-threaded Shaft
The upper part of some long screws’ shafts near the head is usually unthreaded. This is because only the threaded bottom part is needed to produce the friction required for the screw to work. So there is no need to thread it in its entirety.
5. Thread
This is the mechanical part of a screw that is grooved or has a helical or conical spiral on the surface of the screw’s shaft. The pitch of the thread means the distance between the threads.
6. Thread Crest
The crest of a thread means how deep or shallow the grooves are. Depending on where the screw is used, it might require deep or shallow groves to function correctly.
7. Screw’s Thickness
The diameter of the shaft determines the thickness of a screw, while the screw’s thickness will vary depending on the weight it is supposed to hold. In addition, the major diameter is the thickness at its head and the minor at its tip.
How Do Galvanized Screws Work?
Essentially, galvanized screws work the same as plain screws but offer better protection from the elements and rust. For example, when you drill a hole into a metal fixture, you introduce a stress point and a potential point of failure. Then when you use a poor-quality screw like a plain steel one, you compound the effects by introducing rust potential, which can also spread to the rest of your structure.
However, when you use a galvanized screw, you mitigate the chances of rust or corrosion to the screw and structure. So how galvanized screws work is by limiting the possibilities of failures or a potential weak point from a screw.
What Are Galvanized Screws Used For?
Depending on what you’re trying to fasten, you might need different tools for the job. For example, a screw needed to fasten a board in your bedroom’s closet does not require the same corrosion resistance as one used on the roof. Because galvanized screws cost a bit more than plain screws, here are some applications you should use them.
1. Treated Lumber
Treating wood involves forcing chemical preservatives into the lumber via a vacuum and pressure process. This type of wood is excellent for its fungal, insect, and fire-resistant properties, which is good. However, these same chemicals are known to react with plain steel screws and cause them to corrode.
To stop this from happening, use galvanized screws to prevent any corrosion and preserve your structure longer. In addition, the zinc on the steel screw will act like a jacket that protects it from the chemicals.
2. If You Live Near the Coast
The high humidity, heat, and salt-rich air in coastal areas give the construction industry enough to be worried about. These conditions are tough on materials, and it’s always best to use galvanized screws for fastening applications.
Salt, in particular, is a common offender known to wear down steel screws by corroding and compromising their integrity. This tends to necessitate repairs often, but you can mitigate it by using galvanized screws in the first place.
3. Outdoor Applications
Even if you do not live in a coastal area, your outside fixtures still require protection from the elements. If you’re fastening anything outside or that’s going to spend most of its time outdoors, use galvanized screws to prevent rusting.
For example, having your roof’s shingles held in place by galvanized screws would serve you well. However, steel screws will rust in no time, and your shingles might start to come loose and drop off or, even worse, let water into your house. These scenarios would cause substantial damage that you can mitigate by using the proper screws.
4. Outdoor Furniture
Sometimes outdoor furniture is constructed using treated wood, and not to mention they have to withstand the elements. Plain steel screws don’t stand a chance. Unless you prefer making repairs every so often, we recommend using galvanized screws that can take the beating from the weather.
5. Fencing
Creating a sturdy and low-maintenance fence is critical to giving you lasting peace of mind. If you fasten your fence with plain steel screws, they will rust in no time and cause your fence to start falling apart.
However, if you use galvanized screws, the zinc coating on them will protect the steel underneath and preserve its chemical properties. This will help keep your fence standing for a long time and require less maintenance overall.
What Are the Different Types of Galvanized Screws?
Galvanized steel screws, and zinc, to be exact, are the most common type of screws you will find on most shelves. This is because they are relatively cheap to make and offer excellent rust resistance. There are a few ways screws can get galvanized: mechanical, hot dipping, or electroplating. They produce different results that we’ll be looking at below.
1. Mechanically Galvanized Screws
You galvanize screws mechanically by placing them into a drum filled with chemicals such as zinc powder and glass beads. Then you tumble them for a period to enable the zinc powder to adhere to the surface of the screw.
The zinc layer forms a protective coating without exposing the screws to dangers such as hydrogen embrittlement. The zinc layer that occurs is also thick and offers excellent protection. In addition, its smooth, blueish gray color requires little to no maintenance.
The application of this process is typical for screws and metallic parts with high strength requirements. So if you need fastening of structural bits, these are the screws you should consider.
2. Hot Dipped Galvanized Screws
Hot dipping involves using a molten zinc bath to bond the screws with the zinc. Once the zinc bath is up to temperature, you dip the screws in for a few minutes to allow galvanization. You then remove the screws from the bath, let the excess zinc drip off, and cool.
Hot dipping applies the thickest protective coat of zinc of any galvanizing process. The coat is also bluish-gray in hue, just like in mechanical glazing, and requires little to no finishing.
Hot dipped screws are sturdier than plain steel screws as they preserve their properties pretty well, even in harsh conditions. So if you’re doing your roof or other outside applications, consider using these types of galvanized screws.
3. Electroplate Screws
Electroplating is one of the most effective ways of applying a protective layer to any metallic surface, including screws. It involves using a bath with dissolved zinc and a zinc electrode at the anode end of the circuit. You then place your steel screws at the anode end.
When you apply current through the circuit, zinc dissolves from the anode electrode and is deposited on the screws at the cathode end. This forms a shiny uniform coat that is unique to this process.
However, because the coat is usually thinner than in most other processes, it also tends to wear or scratch off easily. This makes these screws unsuitable for applications where they have to deal with a lot of moisture.
Pros of Galvanized Screws
1. Aesthetics
Wood that is put together with galvanized screws has a pleasing aesthetic. This is because galvanized steel has a lovely bluish-gray hue that goes well with woods such as redwood. Not to mention that galvanized steel screws don’t rust. When steel screws rust, they turn really nasty and change the aesthetics of the fixture, which can ruin the whole look. In addition, the rust can affect the rest of the structure.
2. Durability
When you use screws to hold something together, you expect that thing to serve you well and for a long time. Galvanized steel screws are more durable and are way less prone to fail due to exposure. So you can have them in all sorts of conditions and expect them to perform well for a long time.
3. Safety
Because galvanized steel screws are durable and resistant to corrosion, they are much safer than plain steel screws. You’re much more likely to get an infection from a rusted plain steel screw than a galvanized one.
On the other hand, if the screws hold structural bits that are essential for structural integrity, you will get fewer failures from galvanized screws.
4. Corrosion resistance
Corrosion is the most significant culprit that causes failure in screws. It eats away at a screw’s structural integrity and leads to its eventual collapse. To reduce the effects of corrosion, it’s essential to protect steel screws by galvanizing them with a protective zinc coating. The zinc coating, which is much better at resisting corrosion, will take the brunt of the elements and preserve the steel.
5. Recyclable
All the zinc and steel metals used in creating galvanized screws are 100% recyclable. The metal materials can be recovered and reused as is, without requiring additional processes. This reduces dependence on mining, reducing the adverse effects associated with the mining industry.
6. Better Than Nails
Galvanized screws are better than nails as they not only provide a better friction coefficient screw. But they have better corrosion resistance too. In some applications, a half-sized screw would be better than a corresponding nail for fastening a fixture.
Cons of Galvanized Screws
1. Cost
Galvanized steel screws have to go through additional manufacturing processes that plain steel screws don’t have to. This adds to the production cost, which results in a higher price at the counter. So to keep your costs low, know the essential places to use galvanized screws and only use them there.
2. Hard to Paint
When you paint galvanized steel, the paint tends to peel off in time. So when you use galvanized steel for your structure and paint over it, expect to have chipped paint from the screw heads. Depending on how OCD you are, this might not be something you don’t want to deal with.
3. Chipping and Cracking
Galvanized screws’ protective coating can chip and crack, compromising the entire screw. In addition, if the screw is not stored, handled, or installed correctly, the coating will wear off and expose the steel, which can rust. This renders any protective properties from the galvanization process ineffective.
4. Energy Intensive
Melting and keeping zinc baths at temperature or electroplating screws requires a lot of energy. This adds pressure to natural resources and contributes to global warming through burning fossil fuels to meet those energy needs.
Conclusion
Screws might seem like a mundane item that you barely think about when working, but they are essential tools that, in some cases, perform better than nails, and we would all be better off learning how they work. There are many types of screws, and all perform differently depending on their use cases.
Galvanized screws have a zinc coating to help them retain their physical properties even when exposed to harsh conditions.
So, if you’re constructing or looking to fasten something out in the open, use galvanized screws to prevent corrosion and rust. It will serve you better in the long run.
- https://crossroadsgalvanizing.com/2020/03/03/galvanized-steel-vs-stainless-steel-which-is-the-better-choice/#:~:text=Galvanized%20steel%20is%20coated%20with,as%20it’ s%20not%20salt%20water.
- https://homesteady.com/13415180/what-are-galvanized-screws-used-for
- https://www.marshfasteners.com/when-to-use-stainless-steel-vs-galvanized-zinc-screws-for-outside-construction/#:~:text=Galvanized%20screws%20are%20basically%20just,is%20exposed%20to%20the%20elements.
- https://www.woodmagazine.com/materials-guide/fasteners/drive-screws-that-dont-corrode#:~:text=Commonly%20available%20galvanized%20screws%20are,a%20shiny%20silver%2Dcolor%20surface.
Featured Image Credit: Alekskan12, Shutterstock
Contents