What Is Balloon Framing? Advantages, Disadvantages, Types, & FAQ
-
Pete Ortiz - Last updated:
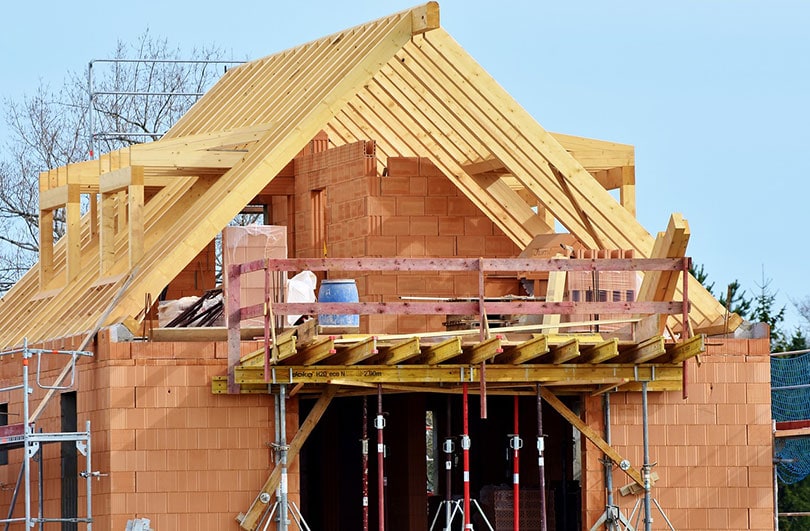
Often, after a hurricane or tornado has torn off houses, you’ll notice that some retain their roofs while others don’t. It’s the result of the type of framing, which is the structure that holds up the floors, walls, and roof, plus the materials used.
Framing systems use dimensional lumber and other structural elements to support the sheathing materials for roofs, walls, and floors. Types of frames include platform, beam, and balloon, the latter being one of the most common in the Americas from the late 1800s to the 1930s.
So, what is balloon framing, and what are its pros and cons? Plus, does it have a modern variant? Read on to find out.
How Does Balloon Framing Work?
As alternatives to mass wall construction, framing systems eliminate heavy material stacking. That’s common in masonry, log cabins, and adobe houses where stacks are layered horizontally.
Balloon framing is a well-known house construction design that was popular in the US and Canada between the 1880s and the 1950s. It can trace its origin in Chicago, and while the story varies, it’s said that George Snow built the first instance in 1832 as framing for a lumber warehouse.
In the absence of construction machinery, balloon framing found favor as a less labor-intensive building technique. That’s because of how fast and inexpensively you could build a house since it doesn’t involve any complex carpentry or joinery.
In balloon construction, a timber frame structure features studs that continuously run from the sole to the rafter place. Instead of mortise-and-tenon joints, wooden elements are joined using nails, and floor members sit directly on the walls.
The building’s outer elements, initially meant for keeping out the weather, also brace the wooden stud walls to increase the load-bearing capacity. Without complexity and with shared and multiple functions, a structure built in balloon framing becomes easier to build and is more efficient.
It’s easy to manipulate materials used in balloon framing, even by hand, and members are lightweight. Fastening avoids joinery, which takes time and skill to create, instead favoring nailed connections that are comparatively simple.
Compared to beam and post construction, a balloon-framed house omits the heavy timber frame, using a third of the wood materials, so it’s erected faster. Using long lumbers and studs, it predominantly used 2×4 and 2×6 beam sizes long enough to build two or three stories high.
One upside of balloon framing is that a home will have high ceilings and walls, perfect for constructing large windows or a tall chimney. The structure construction model also helps in wind resistance, which prevents cracking the drywall and letting in seepage that rusts the nails.
What Are the Different Types of Balloon Framing?
Balloon framing comprises a structure with material pieces nailed together, unlike in a platform frame where floors are framed independently. The technique utilizes vertical members or studs stretching the entire building’s height from the foundation to the rafter plate.
Prominent examples used in the US and Scandinavian countries include the shingle and Queen Anne styles, which prevailed when there was an availability of longer timbers. It was, however, supplanted by platform framing, where each story consists of floor-to-ceiling panels. A deck will be the platform for the next story or roof being built.
The main distinction between these styles is that balloon framing studs run from the foundation to the rafters, while independent studs signify the platform technique. Ligaments hold the structure together, and heavy columns and beams are replaced by continuous framing posts with intermediate horizontal elements.
For the roof, a truss structure consists of ceiling joists and sloping rafters, unlike platform framing, which uses plates or panels to extend the building upwards. Balloon framing is necessary only where the flexibility for large windows, two-tier fireplaces, and a vaulted ceiling is required.
It’s also easier to obtain design features like arched windows using balloon framing than with platform frame construction. The wall created is more resilient to external elements, meaning it withstands high-speed winds, and the structure lasts longer. To increase fire safety, one trick is to use power poles within the walls on each floor, especially for residential buildings.
Before balloon framing became the go-to for building houses, carpenters and joiners had to be experts, especially if the rest of the house featured masonry or bricks.
Platform Framing vs Semi-Balloon Framing
Platform framing is the building technique for structures that replaced balloon framing and is now the dominant method. It uses shorter lengths of lumber with 2×4 studs placed or spaced 16 inches in the center.
On walls, platform framing features a sole plate or sill, two top plates, and studs bearing on the floor joists. It doesn’t require hangers as each story is covered by a platform providing subflooring, a work surface on which partitions and walls are erected.
Walls are constructed on the ground, with platform framing, so there’s less effort in lifting them into place than the balloon frame. Once a story is constructed, you can use framers instead of notching studs to build the next floor. The technique also accommodates prefabricated methods.
Semi-balloon framing is a cross between platform and balloon framing, and it doesn’t have a continuous stud from floor to roof. It also requires hangers, unlike balloon frames, and floor joists hanging from double-top plates.
Platform framing may be the dominant of the two, but semi-balloon frames are standard in structures extending five or more stories. It’s often used as the alternative to the former, especially in the US, where many states follow the international building code.
Semi-balloon framing is preferred where shrinkage or fire requirements are challenging and as an alternative to platform structures. An exception in the code for type 3 construction that requires a non-combustible exterior wall says fire retardant wood or FRTW may be used. That requires hanging joists off top plates to eliminate the penetration of the external wall building envelope.
Balloon Framing vs Prefabrication
As a deficient level industrial building system, balloon framing uses some components of early prefabrications such as dimensional lumber, trusses, roof deck, and nails. It’s a simple method with materials that are easy to combine, but the final assembly takes place on-site, which is time-consuming.
Prefabrication of building elements, especially structural ones, remains elusive outside of a few building types where it’s optimized. By increasing the use of prefabricated elements, there’s an attempt to reduce site work. Still, more significant members must be custom designed to fit specific requirements for the building or site.
When Was the Heyday of Balloon Framing?
It took long after modern construction methods had taken root for balloon framing techniques to appear since industrialization provided requirements in the early 1800s. Initially, there was lumber, which meant enormous work without specialized machinery.
The advent of steam-powered sawmills brought in a solution, and by the 1840s, there were several hundred on the Michigan peninsula. That was an improvement from the earlier water-powered mills that could only manage to cut about 1,500 feet of board lumber in a day.
Another technology emerging in the last part of the 19th century was nails, which initially were hand-forged and expensive to come by. In some cases, abandoned buildings had to be burned down so they could collect precious iron nails.
That was before the industrial revolution introduced steam-powered nail-making machinery. What was once an item amounting to almost 0.4% of the country’s GDP fell in price fourfold as machines produced tens of thousands of nails a day.
Another facilitator to the spread of balloon framing as the desired structure-building technology of the day is railroads. Between the 1820s and 1850s, the US had 9,000 miles of railroad track, increasing to more than 250,000 miles by the early 1910s.
Railroads allowed timber shipping across the country inexpensively. The construction sector used it despite the unavailability of lumber locally. That’s why cities like Chicago continued to rely on regionally sourced lumber even as local forests dwindled, as this material became a national commodity.
America might not be what it is today if there wasn’t the advent of balloon framing, as it allowed homes to be shipped across the country. That was particularly vital in the west where lumber wasn’t abundant, plus construction cost less in time and money. There was a small availability of experts to build houses as almost everyone was a jack of all trades.
How Was Balloon Framing Used in Construction?
As we’ve seen, balloon framing is an example of early industrialized construction, relying on mass-produced machine-made products of a uniform dimension produced in large volumes. Carpenters and builders could replace custom components with interchangeable parts, shifting construction from a skilled specialized craft to repetitive, semi-skilled labor.
Balloon-framed houses are unique because the framing members run uninterrupted from the mudsill to the rafters. It’s, however, fallen into disuse since there’s no longer the wealth of tall old-grown trees that proliferated in American forests, often measuring from 20 to 30 feet long.
Some issues with balloon framing, such as the lack of fire breaks between walls, make it suitable for one-story houses. That means it’s unsuited to multi-story buildings and should be relegated to mission-style and bungalow homes.
It’s easier to know which kind of framing was used in the construction of your house if you open up the walls, floors, and roof. One way to start your search is through the attic, as you’ll notice the second floor or roof’s trussing is held up by ledger boards instead of a top plate.
In a balloon-framed house, there’s direct access from the attic subfloor or second floor down to the basement or stud bay. The break-in-between stories immediately catch anything falling in a platform frame.
While that’s not an exact science, it’s the only accurate test to tell how your house is framed besides opening up the walls during repairs. While inefficient, inelegant, and featuring incomplete systems, the balloon frame technique was more accessible to install than the alternatives, however elegant.
Balloon framing is tedious, and its construction is rife with imperfections since there are no engineering tools for its precision. There are cases where this structure-building method was used earlier than the 1880s, and one of the best examples is the St. Mary’s church built by George snow.
- Rather than borne from rational analysis, wood design is prescriptive and based on what’s historically performed well.
- It’s a tedious process that can’t be fully engineered and is not amenable to mathematical tools for structures.
- Complex connections, indeterminate elements, and circuitous load paths result from fastening small pieces.
- Wood is a highly variable material with hundreds of properties depending on size, grade, and load direction alongside tree species, temperature, moisture content, and drying duration.
- The balloon framing structural system has no simplicity or aesthetic elegance as it’s made up of small flimsy members, leading to imprecision.
Advantages of Balloon Framing
Balloon framing was the technique widely used in North America for much of the early 20th century up until the 1950s. That was when longer timbers were readily and customarily available to build the lightweight, continuous wooden sections extending two or three stories high.
The method entailed scabbing together 2x4s in a balloon-framed structure to achieve the intended height, and often construction was on a tight budget. It significantly reduced the technical expertise and labor required to construct long-lasting buildings.
Since the balloon framing technique doesn’t require sophisticated carpentry, joinery, or a qualified workforce, it gained popularity in the US and Canada.
- Use of simple sockets instead of complicated joints in carpentry and design
- Quick raising of buildings by anyone with basic skills and tools
- Sustainable, renewable, and affordable wood materials
- No demand for large equipment required in moving heavy beams
- Little shrinking potential and the likelihood of building trembling
- Improved load-bearing capacity
- Less drywall cracking, nail pops, and more wind load resistance
- Improved design aspects like large windows with arched, angled, or rounded tops
- Larger rooms, lofty chimneys, and an open entryway past two stories
Disadvantages of Balloon Framing
Balloon framing features light wood studs, rafters, and joists spaced closely to support a continuous line from the base to a building’s roof. One downside of this technique is that longer studying is less efficient to install than the shorter ones used with a platform frame.
There’s also the continuous line of spaces between these studs that act to fan a fire instead of resisting the flames. While the style is easier and less expensive to build, balloon framing has minimal shrinkage and doesn’t allow the plaster to crack.
Balloon framing isn’t the structural system an engineer will design from scratch, and many contractors would fail to follow the plans. There are many extra members with a whole design field for their removal, not to mention the imperfection of gaps and slightly askew elements.
- Without a fire stop between studs, the technique poses no flame retardation
- Compared to platform framing, longer studs take longer to install than shorter ones
- Exposed wooden studs leave vertical hollow spaces, which pose many risks
- Long lumber materials aren’t as available or sustainable
- Labor expenses may increase due to tall gable walls that require scaffolding
- Raising walls or roofs require skilled labor and specialized lifting gear
Frequently Asked Questions (FAQs)
1. Why is this structure construction technique called balloon framing?
The name balloon framing came from the buildings looking flimsy so much that a strong gust of wind might blow them away, like a balloon.
2. Why did balloon framing stop being in widespread use?
The lack of long and lightweight lumber for straight studs led to the disuse of balloon framing. By the late 1910s, sawmills that spread around the Michigan peninsula had exhausted their tall, old-grown timber supply and closed down.
3. Is balloon framing still used by much of the outside world in construction?
While many modern buildings use bricks and masonry, many countries outside North America and Europe use platform or post-and-beam construction.
Conclusion
Balloon framing shines due to its ease of implementation, as it doesn’t require specialized carpenters, joiners, welders, masons, or crane operators. Besides the inexpensive labor, no heavy lifting or erecting machinery is needed, and it can be put together with simple tools and bare hands.
A balloon-framed structured home accommodates services in the voids left between studs, where insulation, piping spaces, and switches may be placed. Since it’s a wood structure, running lines or drilling holes is easy, so you can fasten the utilities you need in your home.
With balloon framing, incomplete or imperfect planning is accommodated, and any mistakes won’t result in cost overruns that are common with prefabs. While you can’t scale up to high-rise buildings, the technique fits simple low-rise residential houses.
You Might Also Be Interested In:
- Origins of the Balloon Framing Structure Building Technique
- Balloon Framing Wood Elements Dimensions
- Balloon, Semi-Balloon and Prefab Method
- Industrialization and the Rise of Balloon Framing
- How the Advent of Railroads Spread Balloon Framing
- Earliest Example of Balloon Framing
- Downsides of Balloon Framing
- Popular Structure Building Styles besides Balloon Framing
Featured Image Credit: Ralphs_Fotos, Pixabay
Contents