What Is Polystyrene? Pros, Cons & Uses
-
Pete Ortiz - Last updated:
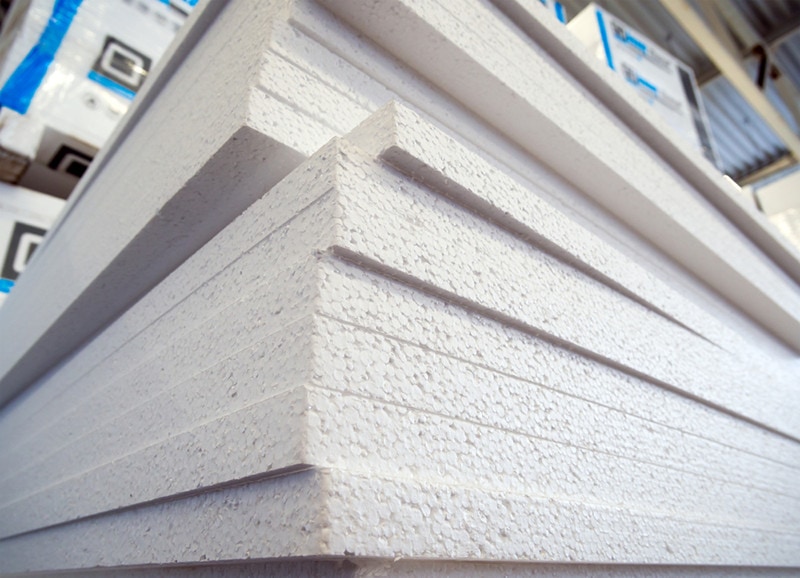
Polymers have been around for ages and have greatly impacted our lives. Cellulose, wool, and silk are great examples of naturally-occurring polymers. And then there are manufactured polymers, including epoxy, Teflon, and, of course, polystyrene. So, what is polystyrene, anyway? How is it made, and what are the common uses for it? The short answer is: it is a synthetic polymer, a plastic. This versatile material is used in packaging, insulation, medicine, and the automobile industry.
Thanks to the cheap manufacturing process, flexible nature, and impressive lifespan, polystyrene is one of the most commonly-used synthetic polymers on the planet. But how does it work, exactly? Are there different types of polystyrene on the market? What sets polystyrene plastic apart from foam? We’ll cover all of that in this guide, along with the pros, cons, and FAQ. Stay tuned!
How Does It Work?
Polystyrene is a synthetic polymer, a plastic. It’s highly flexible and can be easily molded into different shapes. Solid or foamed, polystyrene is an affordable material. Each year, facilities from across the globe produce millions of tonnes of this plastic. Transparent by default, it’s often colored to make it easier on the eyes. General-purpose polystyrene is brittle, yet hard and long-lasting. Technically, it can be recycled, but by ASTM standards, it’s considered a non-biodegradable product.1
Developed back in 1839 by Eduard Simon, polystyrene has been in heavy use since then.2 Over the last 170+ years, scientists from all over the world have been working to improve the original formula. Today, it’s cheap, easily produced, and widely available. Polystyrene is used for producing disposable cups, containers, and cases for CDs, among other things. On top of that, it has decent insulating properties and is commonly applied in construction.
How Is Polystyrene Made?
There are two types of polystyrene, EPS (expanded polystyrene) and XPS (extruded polystyrene). And, while they’re both referred to as polystyrene, the manufacturing process and their properties/qualities do vary. Here’s a more detailed look at both materials and how they are made:
- EPS is crafted from styrene monomers. Styrene is an organic compound: it comes from benzene and ethylene. So, how does it turn into rigid plastic? To convert it into polystyrene, styrene is heated to a temperature of 248°F (that’s 120°C). Thermal processing makes polystyrene grow up to 40–50 times larger. Plus, it makes it softer. For the best results, a “blowing agent” like pentane is added into the mix.
Once the tiny beads of styrene expand and fuse, they are placed into molds and heated once again to fill out the mold completely. This is known as block molding: the large blocks are then cut into smaller boards. Shape molding is another practice where the polystyrene is custom-shaped. This is often used for packaging expensive electronic devices/products. EPS doesn’t contain any harmful chemical compounds and takes little effort to make.
- XPS relies on a continuous extrusion process to manufacture closed-cell foam. It starts with polystyrene resin granules put into an extruder. There, they are mixed with additives, melted, and converted into a thick fluid. Next, similar to EPS, a blowing agent is added to help the polystyrene expand. So, how is XPS shaped? Manufacturers use a die and specific heat and pressure levels to shape this material.
XPS is sturdier, stronger, and more resistant to water and oxygen vapors than EPS. On top of that, it has a higher melting point (200–210°F vs. 165°). XPS boards differ in comprehensive strengths and are produced to meet the needs of various projects. This polymer is used to insulate areas that are prone to high levels of humidity. It doesn’t absorb water but rather blocks it.
What Are the 3 Different Types of Polystyrene?
Now that we covered the differences between EPS and XPS and how they are produced, it’s time to talk about the various forms of polystyrene:
1. Polystyrene Foam
A classic example of polystyrene foam is Styrofoam. Also known as the “Blue Board”, it’s one of the most popular insulation materials in the US. But that’s not the only application for it. Foamed polystyrene is often shaped into packaging/food containers, single-use cups/plates, and more. And then we have packing peanuts. Lightweight and soft by design, they are a go-to material for packaging.
If you’ve ever opened a shipment box with fragile stuff in it (like something made of glass or electronic components), then you know what packing peanuts look and feel like. Manufactured from EPS, they do a decent job of protecting expensive and brittle objects from impact damage during transportation.
2. Polystyrene Plastic
Do you know what a copolymer is? Earlier, we learned that polystyrene is made from styrene monomers. Well, a copolymer is a combination of two different monomers. On its own, plastic crafted from styrene isn’t particularly hard or sturdy. But when mixed with specific materials or compounds, it becomes more reliable and less fragile. The resulting product is called HIPS, which stands for High Impact Polystyrene.
3. Polystyrene Film
If you’re looking for a strong, clear, and transparent film, polystyrene will be a great choice. PS turned into film tear-resistant, glossy, and easy to print on. On top of that, it has above-average moisture vapor and oxygen transmission rates, which is very important in food packaging and other industries. Add a low production cost and a relatively simple manufacturing process and you’ll see why this product is so highly valued across the board. Polystyrene film is weak against chemicals, though.
Where Is It Used?
With this synthetic polymer, the sky’s the limit. It’s so widespread that we bet you have at least one or two examples of polystyrene back home. Disposable cups, plates, food containers, plastic CD/DVD cases, audio/video cassettes, and packaging peanuts are all crafted from polystyrene. And then you have toys and computer housing. In medicine, polystyrene is used for diagnosis components, test tubes, and more.
In construction, EPS and XPS serve as cheap, long-lasting insulation materials. Polystyrene’s thermal insulation properties find their use in fridges. In the automobile industry, this plastic is used to manufacture the instrument panel/dashboard and the door knobs. Air conditioners, microwaves, and blenders also have parts made of this plastic.
Advantages of Polystyrene
- Cheap, wide range of applications. Very few plastics are as affordable as polystyrene. It’s manufactured from hydrocarbons (ethylene or benzene) that come from natural gas and petroleum. Polystyrene is one of the most flexible, accessible, and in-high-demand materials ever to exist. And, since it’s synthetic and produced at man-made factories, shortages or unexpected price spikes rarely happen.
- Durable, great at insulation. Polystyrene foam is quite durable and has excellent insulating properties. It contains a huge number of air bubbles that prevent heat from escaping. For extra efficiency, go with XPS: it has a denser structure. And that’s why it’s a go-to choice for foam insulation in residential and commercial buildings.
- Strong against water/moisture. In many ways, EPS is like Rockwool: it’s resistant to humidity, yet if water goes through, it does get wet. XPS is a lot more water-resistant. It absorbs less water and prevents it from seeping into the walls. XPS has a water vapor diffusion resistance of 80–250; EPS only has 30–70.
- Lightweight, easy to work with. If you’re trying to insulate an entire house on your own, the lightweight nature of polystyrene will be a big pro. Not only is it easy to work with, but it’s also not heavy. If you cut it into relatively smaller pieces, that will make working with EPS or XPS easier (just like it would with fiberglass or mineral wool).
- Harmless to h Cups, plates, trays, and food packages crafted from polystyrene may contain tiny bits of styrene. However, according to the FDA, polystyrene is 100% safe to use and doesn’t pose a threat to the health of human adults or children. The amounts of styrene in EPS are 10K times below the FDA safety limits.
Disadvantages of Polystyrene
- Relatively low melting point. We use the term “relatively” because, for most applications, polystyrene is considered a fire-resistant plastic. That’s right: the 165–210°F melting point is more than enough for most applications. That said, if you’re looking to fireproof a house or commercial building, it won’t be the best choice. Stone, bricks, concrete, and steel will be far better picks.
- Poor chemical resistance. It doesn’t really matter whether it’s EPS, XPS, film, foam, or plastic—polystyrene is weak against a wide range of chemicals. Mainly, we’re talking about ethers, esters, ketones, and, of course, hydrocarbons. That’s why it takes forever to decompose in a natural environment.
- Brittle; easy to break. This is only true for polystyrene plastic. The film and the foam are quite sturdy. Besides, they’re used in slightly different applications. Going back to plastic, if you’re careful, it will serve for many years. Besides, this is a cheap material that won’t cost much to replace.
Frequently Asked Questions (FAQs)
How long does polystyrene last?
One of the best things about this polymer is its long-lasting nature. For example, if you use polystyrene insulation in your house, you won’t have to worry about it for the next 4–5 decades. In fact, many foam boards crafted from polystyrene are backed by a 30–50 year warranty by the manufacturer, which speaks volumes about their service life. As long as it’s not exposed to extreme heat, chemicals, or physically damaged, it will last for the life of the house.
Is polystyrene recyclable? How do you dispose of it?
There’s no quick answer to this question. The important thing to remember is that polystyrene takes a VERY long time to decompose. We’re talking about 500 to one million years here! So, when put in a landfill, this cheap material doesn’t go anywhere. As a result, we see huge amounts of plastic washed up on shores around the US and the rest of the world. On the bright side, as a polymer, polystyrene can be recycled.
It does take expensive equipment to do that, though, and there aren’t nearly enough facilities out there that can handle EPS or XPS. That’s why it’s often recommended to put it in the waste bin. Crafted from petroleum, it’s not a renewable product; therefore, it’s categorized as unfriendly to the environment. Polystyrene does break down rapidly when mixed with various hydrocarbon compounds, however.
Polystyrene vs polypropylene: What’s the difference?
Let’s start by saying that both materials are polymers. However, while polystyrene is made from styrene, polypropylene is crafted from propylene. The manufacturing process is different as well. And what about the common uses? We already learned that polystyrene is used for making kitchen appliances, cups, containers, auto parts, and stuff like that. Well, polypropylene is also a go-to material for containers, packaging, and car parts.
However, it’s more often used to produce pipes, bottles, and test tubes. Polypropylene is more lightweight, highly resistant to cracks and organic solvents, and boasts a higher melting point (266–340°F). Another big pro: it’s significantly sturdier than polystyrene. At the same time, EPS and XPS are cheaper and more widely used, especially in the food and packaging industries.
When to Go With Polystyrene | When Not to Go With Polystyrene |
You need a cheap, long-lasting synthetic | You’re looking for an eco-friendly synthetic |
Water resistance is a top priority | Fire resistance is of great importance |
You want to insulate your house/room | The project requires sturdy materials |
You’re looking for a lightweight material | Low chemical resistance is not acceptable |
- Related Read: Is Thermocol Recyclable? How Is It Properly Disposed Of?
Conclusion
As far as the most important man-made polymers go, polystyrene is right on top of the list. It’s been around for decades and has proven to be the best material for a wide range of applications. It takes little effort and financial investments to make. Polystyrene carries incredible value and makes our lives easier and more enjoyable.
Plastic cups, food packaging, CD jewel cases, and house insulation are all made of polystyrene. This synthetic can be recycled, too. On the downside, it’s flammable, weak against certain chemicals, and very easy to break. Still, the pros strongly outweigh the cons, and that’s why polystyrene will continue to be the most commonly used plastic on the planet!
Featured Image Credit: VPales, Shutterstock
Contents