What Are Wind Turbine Blades Made of? Materials, Alternatives, & FAQ
-
Pete Ortiz - Last updated:
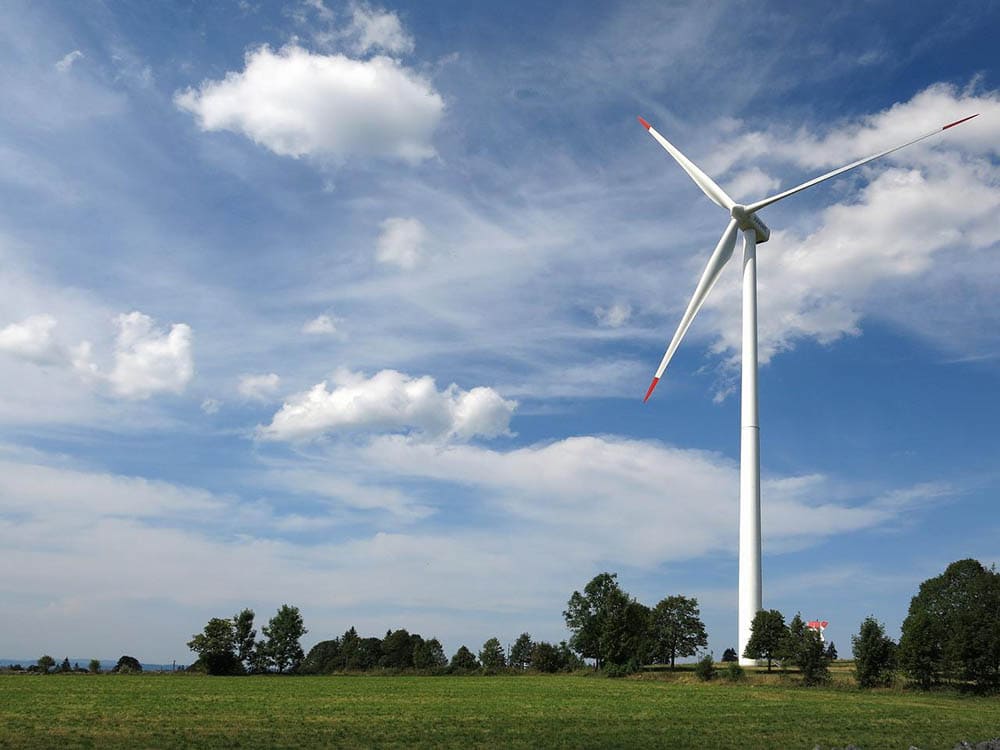
As an essential component of the global shift toward renewable energy, wind turbines continue growing in use and scale. Today’s onshore turbines tower over 300 feet high, supporting blades up to 164 feet long and generating over 6 million kWh of electricity each year. Because power increases with longer blades, the plan is to make the gigantic structures even more massive in the coming years.
Creating a durable, efficient mechanism bearing those enormous wind-catching blades is challenging. While the tower is a heavy-duty, tubular steel support, the blades consist of E-glass fiberglass mixed with a binding polymer. The composite is lightweight yet strong, allowing the blade to spin with less wind force and reducing stress on the tower.
Unfortunately, the wind turbine blade materials aren’t as green as the energy they produce. End-of-life disposal has created unique issues for eco-conscious industry leaders in recent years. Recycling opportunities and novel designs are the current focus of a push to manage a growing sustainability problem.
What Are Wind Turbine Blades Made of?
The most common configuration for onshore and offshore wind turbines is the horizontal axis wind turbine (HAWT). These feature 2–3 aerodynamic blades fitted on a rotor. The rotor connects to a generator within a horizontal nacelle. Sitting atop the tower, the nacelle rotates to keep the blades pointing upwind or downwind as needed to make them operate.
A wind turbine blade includes several materials to improve stability, reduce weight, and add protection. The shell and spar cap, the blade’s support layer, consist of a fiberglass mesh bonded with resin. Older blades utilized a polyester resin, but most of the industry switched to epoxies as turbines got larger.
The blade’s inner structural girder is either a box beam or shear webs. There are two parallel I-beams that fill the cavity between the sides of the shell to give them support.
- Lightweight core material such as balsa wood or polyurethane foam on the blade’s trailing side
- Metal foil for lightning protection
- Polyurethane paint and epoxy gelcoat for protection from wear
Three separate components combine to form a wind turbine blade—two aeroshells that close together around a shear web. Fibers sit in a mold that fills with resin under a vacuum, creating the two halves of the shell. Blades then go through a high-temperature curing process before assembly. After passing a quality check, assembled blades can head off to the wind farm.
Fiberglass Composite Alternatives
Fiberglass is the primary material for providing lightweight structure because of its cost-effectiveness. But as technology evolves and turbine blades increase in size, a need for more durable materials is emerging. Manufacturers have tested several alternative fibers to improve blade strength, including:
- Aramid
- Basalt
- Natural materials (e.g., jute, hemp, bamboo)
- Hybrid materials
The most attractive alternative is carbon fiber, which is already showing up in spar caps, shear webs, and other blade components. Carbon fiber has a lower density and greater stiffness and fatigue resistance. It can make blades larger, lighter, and longer-lasting.
Despite clear advantages, carbon fiber hasn’t caught on in greater use because of its cost. Most manufacturers limit its inclusion to spar caps, but new carbon fiber sourcing may allow for its expanded use.
One viable option is a heavy tow carbon fiber pulled from acrylic fibers used in the textile industry. It is 57% less expensive than the industry-standard carbon fiber but offers 56% more compressive strength. Sturdier than fiberglass, this kind of carbon fiber can lower fatigue while delivering a 25% reduction in blade mass.
What Is the Lifespan of a Wind Turbine Blade?
Wind turbine blades last 25–30 years. Carbon fiber can extend the lifespan of blades since carbon fiber spar caps last up to 63 years. Fiberglass has a typical lifespan of only 32 years.
Still, fiberglass is the current king of wind turbine blade construction, as it has been since wind turbines began to catch on in the 1990s. Many original wind turbines and blades are approaching the end of their 25-year lifespans. In an ironic twist, these “eco-friendly” energy sources are creating new waste problems to solve as they come down.
Are Wind Turbine Blades Recyclable?
Wind turbines are primarily metal. Up to 79% of a turbine’s mass is steel, while iron, copper, and aluminum account for another 6–20%. The metals appear throughout the turbine between the frame, gearing, and electronics. Luckily, most of these parts are recyclable when the structure is ready for replacement.
Because they consist of fiberglass composites, blades are nowhere near as easy to repurpose as the rest of the wind turbine. The majority end up in storage or buried. A large machine cuts the blades into pieces on-site to make them easier to transport to their final resting place in a landfill.
The Future of Wind Turbine Blade Recycling
Right now, about 8,000 blades come down annually in the U.S., each weighing 7–8 tons and spanning over 150 feet. With the eagerness to pump out more power today, providers are replacing many of them much sooner. Blades may only be in service for 10 years before making way for more advanced models.
As more turbines come down each year, companies are setting goals and finding innovative ways to reduce the inherent waste:
- Global Fiberglass Solutions created a process to recycle 99.9% of a blade into pellets for injection molding
- GE partnered with Veolia to recycle shredded blades to make cement
- A USA/Ireland/N. Ireland partnership is working on repurposing blades for powerline structures and roofing
Another area of exploration involves making the wind turbine blade material more eco-friendly. One intriguing example already in use is the RecyclableBlade from Siemens Gamesa. The blade uses a novel epoxy that can dissolve at low temperatures. Once the resin breaks down, manufacturers can separate and repurpose the various fibers, metals, and other components, along with the binder itself.
Final Thoughts
Wind-generated power has grown an average of 12% annually from 2010–2020. Second, only to hydroelectric in global power production, wind power is one of the fastest-growing energy sectors. In 2020, it accounted for 50% of new clean power installations. Given their vital role in reaching net-zero, solving the blade sustainability problem is critical.
Companies like Vestas, GE, and Siemens Gamesa are answering the call. From creative repurposing of old blades to innovative recyclable materials in new models, solutions are in place to reach a circular economy sooner rather than later.
- Science Direct
- “Materials for Wind Turbine Blades: An Overview”
- EIA
- EIA
- Bloomberg
- Scientific American
- Kleinman Center for Energy Policy
- S. Geological Survey
- Machine Design
- “Optimized Carbon Fiber Composites in Wind Turbine Blade Design”
- American Clean Power
- University of Michigan
- Energy
- CNBC
- Iberdrola
- Union of Concerned Scientists
Featured Image Credit: b1-foto, Pixabay
Contents