10 Different Types of Epoxy Flooring (With Pictures)
-
Shea Cummings
- Last updated:
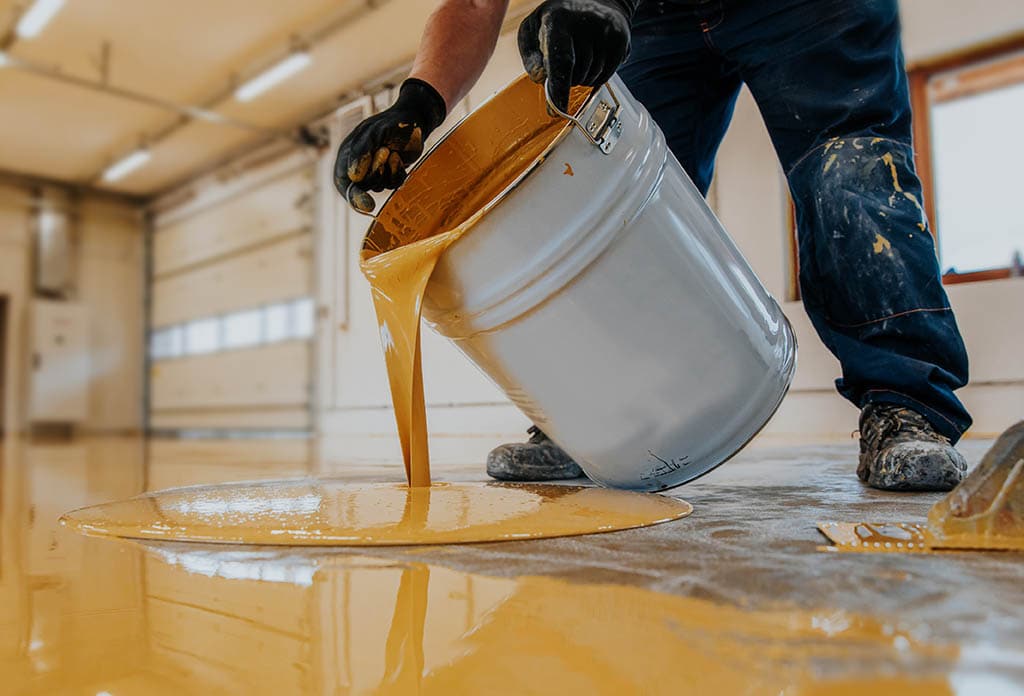
When many people think of epoxy, they probably think of ultra-cool custom tables and counters made from live edge wood and colored epoxy. That is a testament to the versatility of epoxy because it is probably most often used as a floor finish or coating—just about every concrete floor will have a type of epoxy coating of some kind. Below you’ll find ten of the most common epoxy floor coatings out there.
The 10 Different Types of Epoxy Flooring
1. Water-Based Epoxy
Common Uses: | Residential basements |
The benefit of a water-based epoxy is that it has almost no solvents in it. As a result, its volatile organic compound (VOC) content is very low. This low VOC is ideal in residential situations and a great solution in some commercial settings. Another benefit of water-based epoxy is that it can be applied to recently poured concrete that is still curing. While this type of epoxy has come a long way in its technology, it’s not as durable or chemically resistant as a solvent-based epoxy.
2. Solvent-Based Epoxy
Common Uses: | Garages or parking structures |
A solvent-based epoxy is one of the main go-to’s for epoxy flooring in many commercial and industrial settings. If the goal is a highly durable and glossy finish without any other special considerations like antistatic, then a solvent-based epoxy is ideal. A big reason that this type of finish is great in a garage or parking structure is because of its resistance to damage from oil and gas products.
3. Solids Epoxy
Common Uses: | Heavy commercial and industrial use |
Unlike water or solvent-based epoxies, solids epoxy contains no water or VOCs. Essentially a solids epoxy will be a two-part epoxy that consists of a resin and a hardener. When combined, these two ingredients create a chemical reaction. As this reaction takes place, the epoxy cures instead of drying. This means it gets harder over time. A solids epoxy is exceptionally durable and resistant to chemicals and other harsh compounds. Even in a heavily used area, a high-quality solids epoxy will last for years when applied to a properly prepared concrete floor.
Find a flooring specialist in your area, and get free, no-commitment estimates for your project.Consult a flooring expert
4. Antistatic Epoxy
Common Uses: | Electronic and telecommunications industries |
In addition to providing a seamless surface that is resistant to chemical spills, an antistatic epoxy still has decorative properties as it can still be colored like other epoxies. What sets this epoxy apart from others is that it typically has a particular compound in it that draws in static electricity and allows it to dissipate. This is why this type of epoxy coating is common in settings where static electricity discharging can be damaging or even dangerous.
5. Self-Leveling Epoxy
Common Uses: | Commercial and industrial settings—especially on uneven floors |
Most epoxies are rolled on with high-quality rollers. Generally speaking, an epoxy floor will be seamless. But if it is applied by an inexperienced person or with low-quality equipment, seams or inconsistencies can show. A self-leveling epoxy is actually designed to pour, so there is no chance for seams. This is especially helpful if there are uneven areas on the floor where pouring the epoxy will make up for the unevenness.
6. Gravel Epoxy
Common Uses: | Decorative floors or patios |
Typically, you will find a gravel epoxy floor as an outdoor patio floor or driveway. Although, with some ambition, it could be done as a basement floor as well. Often, a water-based or self-leveling epoxy will be used for the epoxy or “binder” for the gravel. Whatever gravel is chosen is spread out flat over the area to be epoxied. Then the epoxy is poured over it. Depending on the particular application or goal, enough epoxy can be used to create a flat surface that submerges the gravel, or just enough can be poured to bind and coat the gravel.
7. Mortar Epoxy
Common Uses: | Heavy use and floor repair |
Mortar epoxy is commonly used in tile work due to the ability to add colors to it and how fast it sets to full strength. It’s very expensive, so it’s not often used to do large floor areas unless the absolute highest durability is needed. Because of how strong it is, mortar epoxy is also commonly used to repair cracks in a concrete floor before applying a final epoxy finish, such as decorative flaked epoxy, for example.
8. Self-Dispersing Epoxy
Common Uses: | Warehouse or potentially wet floors |
Generally, epoxy has a shiny or glossy sheen once dried, so one would assume it is slippery. While some epoxy finishes can be slippery when wet, self-dispersing is commonly used as a non-slip epoxy finish. The reason for this is the quartz sand that is mixed into the epoxy. Not only does the sand give it non-slip characteristics, but it also adds to the mechanical durability. So it would stand up to heavy machinery use in a warehouse, for example.
9. Vapor Barrier Epoxy
Common Uses: | High moisture floors |
Moisture can seep up through concrete floors even after many years of curing if the concrete is poured into a high-moisture area. This moisture can potentially damage whatever sealant was used or furniture on the floor as it seeps through. A vapor barrier epoxy is beneficial in these situations. Before applying the final epoxy, the vapor barrier epoxy is poured to prevent moisture from coming through.
10. Flaked Epoxy
Common Uses: | Locker rooms or arenas |
A flaked epoxy typically consists of a clear epoxy poured over a prepared concrete floor. While the epoxy is still wet, colored flakes are put in it. This does two things. First, it adds an utterly custom-colored style and look because the flake customizations are just about endless. Second, it creates tiny grooves and dents in the epoxy finish that assist in making it non-slip without adding sand.
Is Epoxy Flooring a DIY Task?
There are many DIY epoxy kits on the market. So if you need to refinish your basement or your driveway, there’s no need to call a professional. However, it’s important to follow the directions carefully, especially regarding preparation. Not only does the finish of epoxy rely heavily on proper preparation, but if you haven’t got your ducks in a row once you mix the epoxy, it could start to dry or cure before you have it done. Then you get an uneven finish, and it won’t even cure properly in some cases.
- See Also: What Is the Best Wood for Epoxy Tables?
In Conclusion
So, whether you’re doing it yourself or calling in an expert, now you know what options are available. Keep in mind that some of these epoxy finishes are not applicable to the average person. That being said, if you have the budget, it may be worth checking out an ultra-durable finish like mortar epoxy for your basement—you’ll likely never have to refinish it as long as you own the house.
Featured Image Credit: Doralin Samuel Tunas, Shutterstock
Contents