What Is a Pan Head Screw? Types, Advantages & Disadvantages
-
Pete Ortiz - Last updated:
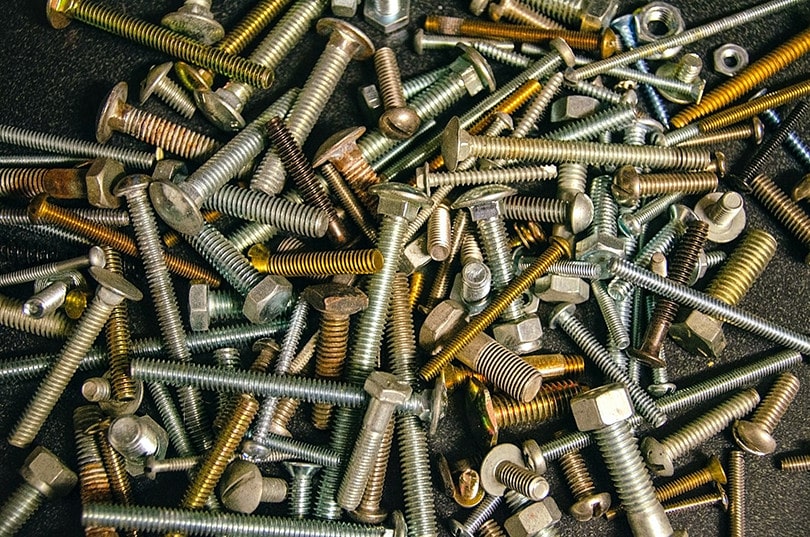
A pan head screw is a type of fastening with a large, circular head. It does not have any sharp edges for safety and visual appeal. There are several, albeit limited, types of pan head screws available, including standard screws with a simple ridge socket for fastening. Machine pan head screws can have a hexagonal socket, and there are wide pan head screws that have a greater load dispersal that prevents the screw head from becoming lodged in the fastening material.
Pan head screws are rarely used in woodworking and commonly used in metalworking where an attractive but secure fastening is required.
How Does It Work?
A pan head screw is similar to any other type of screw. It has a threaded body and a socketed head. It is a non-countersunk screw, which means that the head sits on top of the fastening surface and disperses the working load across the work surface. This helps prevent damage to the surface and prevents the head from becoming buried.
Although a pan head screw has a domed top, the sides are straight so that the head protrudes from the work material. This is unlike button head screws, which curve all the way to the bottom of the head.
What Are the Different Types of Pan Head Screws?
The pan head screw is a type of non-countersunk screw commonly used to finish metalworking projects. Varieties include:
- Self-Tapping vs. Self-Drilling Screws – Pan head screws can be self-tapping screws, which means that they can tap their own heads and can be screwed into a work material. However, they still require a pilot hole before they can be screwed. Self-drilling screws can create a pilot hole and be screwed in.
- Different Screw Head Types – There are four main types of socket head: slotted, which has a single slot and works with a standard screwdriver; Philips, which has a plus-shaped socket and works with Philips screwdrivers; the square-head screw, which is more common in Canada and has a deep square-shaped socket for extra torque; and hex heads, which have a star-shaped socket with six points of contact and plenty of torque.
- Machine Pan Head Screws – Machine screws hold pieces of machinery together, rather than flat work surfaces. These typically work with existing screw holes and cannot tap or drill holes themselves, although there are exceptions.
- Wide Head Pan Head Screws – Some pan head screws have a wider head and are designed to offer even greater working load dispersal than standard pan head screws. These are used when more loads will be placed on the materials, and therefore the fastenings, to ensure they remain stable and secure.
Where Is It Used?
Pan head screws are non-countersunk, which means that they are ideal for use with metal and machine parts where the working surface cannot be damaged or compromised in any way. They also tend to be used for their aesthetic appeal. They are polished and can form part of the design of the item.
Common applications for this type of screw include fastening machinery components, as well as in metalworking. They can incorporate a secure fastening for those applications where vandalism is a threat, and you can see pan head screws used to attach license plates to cars as well as to attach components inside the car.
Advantages of Pan Head Screws
Although pan head screws are not ideal for all applications, they do hold certain advantages over other types of screws:
- Non-Countersunk – The pan head screw is designed to be non-countersunk, so it protrudes from the materials being fastened. This is ideal for use on metal and in machinery where sinking the screw head can damage the material.
- Load Dispersal – The large, flat underside of the screw head sits evenly against the fastened material. This spreads the working load across the area covered, reducing the likelihood of damage to the surface and helping ensure the fastening stays tight and secure. Although pan head screws are commonly used in metalworking, they can be beneficial in woodworking where a countersunk screw may split the wood. The load dispersal across the head of the screw means that damage to the wood should be minimal.
- Attractive Finish – Most pan head screws have a polished or worked finish. This style of screw is used when the screw itself is visible because it has a greater aesthetic appeal.
Disadvantages of Pan Head Screws
Because of the wide range of different types of pan head screws available, they have a lot of potential uses with minimal disadvantages:
- Protrusion – The head of the pan head screw is designed to protrude from the work surface. This means that this type of screw is not suitable where the surface of the finished piece needs to be perfectly level and flush.
Frequently Asked Questions (FAQs)
What Is the Difference Between Flat Head and Pan Head Screws?
Flat head screws have a flat top and a tapered underside. They are designed so that the head sits on the work surface with the head flush with the material. Pan head screws have a flat underside, straight head edges, and a domed top. They are designed to sit on top of the work surface and not dig into the wood or metal below.
Are Pan Head and Button Head Screws the Same?
Button head screws have sloped sides. They slope all the way to the base of the screw head, whereas the pan head screw has straight sides but a domed top. Button head screws do not usually protrude as far from the surface as pan head screws and they can accommodate a larger socket, so more torque can be applied and a stronger fastening achieved.
What Are the Four Different Types of Screw Heads?
- Slotted – The slotted head has a single, etched line, into which a standard screwdriver head is placed. The biggest problem with this type of screw head is that the screwdriver will tend to slip from the socket when a lot of torque is applied. This can make it difficult to achieve a firm fastening and can make it difficult to apply enough pressure to remove the screw later.
- Phillips – The Phillips head has a plus-shaped socket. Because there are four points of contact, more torque can be applied to this type of screw head for a tighter fastening. This type of screw is arguably the most common.
- Square – Square heads have a square hole and are used with a square-headed socket set or screwdriver. The socket is usually deep so that the screwdriver head is virtually immovable once in place and this allows for a lot of torque to be applied.
- Star – The star head has a 6-pointed, star-shaped slot. It offers similar benefits to the square head, except that because it has six points of contact rather than four, even more torque can safely be applied.
Conclusion
Pan head screws are a type of non-countersunk screw commonly used in machinery and metalwork but also used in woodworking where there is the risk of damage to the wood from countersunk screw heads. The head has a flat underside and flat sides, but a domed top and rounded edges. Various screw head styles, and even some specialist coated pan head screws, are available, and this type of fastening offers the benefit of load distribution across the head that can improve stability and fastening strength, while also being aesthetically pleasing.
- See also: 7 types of hacksaw frames and blades
- https://home.howstuffworks.com/pan-head-machine-screws.htm
- https://www.instructables.com/Types-of-Screw-Heads/
- https://www.accu.co.uk/p/150-the-benefits-of-pan-head-machine-screws
- https://fastenerengineering.com/what-are-pan-head-screws/
- https://www.accu.co.uk/p/150-the-benefits-of-pan-head-machine-screws
- https://www.bhamfast.com/self-drilling-vs-self-tapping
- https://www.electronicfasteners.com/pan-head-screws
- https://home.howstuffworks.com/pan-head-machine-screws.htm
- https://uk.rs-online.com/web/generalDisplay.html?id=ideas-and-advice/socket-screws-guide
Featured Image Credit: Robert Ruggiero, Unsplash
Contents